Condition-Based-Maintenance (CBM): The leading edge of proactive sustainment
Defense Maintenance & Sustainment Summit
(DMS 2012)
February 27-29, 2012, | La Jolla, California
It was my first time attending WBR’s Defense Maintenance & Sustainment Summit, and it was fascinating to hear about best practices from the many government attendees and their commercial partners.
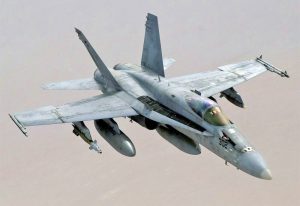
With its first flight in 1978, the F-18 Hornet is a prime example of legacy, military applications still in use today. With a lifecycle of over 30 years, it has been the demonstration aircraft for the Blue Angels, since 1986.
The focus was CBM (condition-based-maintenance), a sustainment approach that involves installing sensors onto defense equipment, and then remotely monitoring the actual performance of critical systems within a fielded craft – such as a plane or land vehicle.
So why is this so interesting?
From a techie perspective, having all this data back at “the base” in near real-time enables the maintenance team to analyze data to predict equipment breakdowns. For example, it’s possible to predict when a truck’s transmission is likely to fail if you can monitor operating temperatures and mechanical wear over its lifetime. From a soldier’s perspective, why is THIS so important?
Maintenance depot crews can mitigate breakdowns by proactively servicing at-risk equipment, which in turn enables the supply chain to more predictably deliver quality parts to the depot. For the warfighter, they will always have a truck…and those trucks will be reliable.
This is another one of those Star Trek concepts that has become a reality – no doubt Scotty and Geordi knew when their warp core was operating at low efficiency. And in reality today, last decade’s leaps in COTS micro-sensor, wireless, and information technology are now time-proven commercial solutions. The challenge now faced by CBM evangelists in the defense industry is how to make a compelling business case for including this additional CBM investment into new and existing applications.
I have confidence program managers will justify the CBM business case. CBM is a practical method not only to raise confidence in reliability predications but also to monitor equipment in real time. This data provides the basis for reducing the number of “spares” and more effectively managing the entire program.
At GDCA, we’re committed to sustaining defense applications for as long as they are needed. We do this by solving and preventing electronics obsolescence issues, and we recognize CBM as another excellent and complementary method to help everyone deliver on this commitment.
Ethan and the GDCA Team